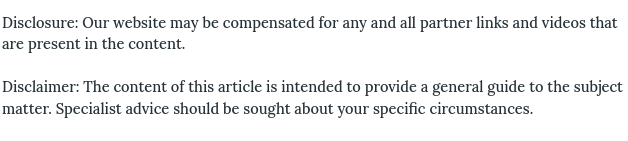
From tumbling drums to vibratory screeners, the use of these tools are able to provide a great deal of manufacturing services in various industries, from the food industry to other industries of the manufacturing world for the production of various good.
Tumbling drums and vibratory screeners can be used for plastic parts, a big use for many vibratory screeners and other such machines here in the United States, where plastic is highly utilized. These tumbling drums and vibratory screeners can be used to polish plastic pieces, when they are tumbled from anywhere from ten hours to fifteen hours at a relatively low speed (as plastic is typically a very light material and does not need particularly rough or intense handling). A tumbling drum and vibratory screeners can also be used as a food crusher – and even as a cement crusher.
But the way that you use tumbling drums or vibratory screeners will vary from use to use, and it is really important to understand these limitations and differences in use of such machines. For instance, you will need to be careful about the actual barrel load. Typically, you should never fill the total barrel load past fifty percent, as this can impede the function of the tumbling done or vibratory screener. You should have a ratio of about three parts of the machine, or media, to every one part that is, to put it simply, being tumbled, as this can prevent the parts that are being tumbled from damaging one another or even the tumbling machine itself. Your barrel should never have sixty percent or more capacity, but it should also never be less than at forty five percent capacity when it is in use, as both of these can impede the effectiveness of the machines. While more action can be obtained with very small loads that are under a capacity of forty five percent, the overall finish will end up being poorer and certainly not as high quality. However, the size of your barrel will itself determine how many objects you can fit within it, and there is no one set number of objects that make up the perfect load, as different barrels for tumbling machines and vibratory screeners will come in different sizes. It will also be dependent on the fragility of the parts that are being tumbled, as well as the shape and the weight of the parts. The total outcome of the finish will also depend on how much the barrel is filled as well. A good rule of thumb, however, is to fill up a barrel about one third of the way for the best and most optimal results.
The speed of the barrel is also something to consider and something that is more likely than not to vary based on the type of barrel, the size of the barrel in use, and the type of material that is being put into the barrel. In general, however, there is a typical range for which barrels are most often kept between. Typically, the barrel speed will not drop before twenty eight RPM, but will not exceed thirty two RPM, though there will be extenuating circumstances for each, depending on the material that is being tumbled.
The time that things will be tumbled will also significantly change from application to application. Some tumbling sessions, for instance, can be as short as six hours and still have the optimal result desired. On the other hand, objects can sometimes need to be tumbled for as many as twenty four hours, an entire full day’s worth of time. Most tumbling times, however, are likely to fall somewhere in between the two times – not as short as six hours but not as long of a tumbling time as twenty four hours. For instance, the plastic tumbling that is discussed above is typically tumbled for no less than ten hours and no more than fifteen hours, often tumbled at a happy medium between the two.