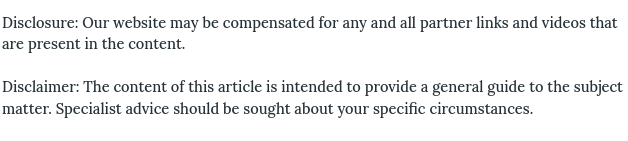

Safety at work should be a top priority for every company. Slowly but surely, it is becoming just that. Where once employees were told to stay safe in quick training sessions, now many companies with hazardous environments are taking fall protection extremely seriously. There are many different types of falls that the right kind of equipment and fall protection training can prevent. There are classic slip and fall incidents, and also falls from great heights — in which case equipment like slings becomes particularly valuable. But equipment and fall protection training on their own are not enough — people need to be trained in the most efficient, professional manner possible. With that being said, many companies are choosing OSHA fall protection training to keep their employees safe. OSHA is, after all, the expert on employee safety, and can provide training that will be both beneficial to the employer and the employee. Rather than wasting your time on an outdated program, you can move forward with OSHA fall protection training and be sure that the strategies you’re employing have been extensively tested and are much more likely to work. Below, we’ll look into OSHA fall protection training and the equipment that could save employees’ lives.
OSHA Fall Protection Training: The Basics
Again, it’s important to stress that employees are not the only ones who should undertake this training. Employers should do the same, in part because their preventative efforts are what will make a real difference. This training is rigorous and extensive, and will not allow for the same casual approach as older training methods did. When it comes to preventing falls and saving lives, OSHA has a three-step process: plan, provide, and train. While you can provide all the equipment you want, you will only be truly prepared when you and your employees know about how to approach a dangerous situation as safely as possible. If your employees are ready and aware, they will be less likely to make mistakes and more likely to stay unharmed. While accidents always happen, you don’t have to accept this and move on — you can make a real difference by being proactive. Keep an eye out for any equipment that looks old or outdated. Double check railings and ladders for any weaknesses, and for that matter when looking into overpasses in warehouses, be sure that they are sturdy and supported.
Safety First: When To Provide Fall Protection Equipment
OSHA has strict guidelines regarding fall protection equipment. This does not mean that it’s required everywhere. If a worker is six feet or more above the ground while working, however, they are at serious risk of injury or death should they fall. In this case, the right kind of safety gear — including scaffolds, ladders, and more — needs to be provided. However, OSHA’s requirements get more detailed than just that. Safety equipment must be provided at levels of four feet in general industry workplaces, five feet in shipyards, six feet in the construction industry, and eight feet in longshoring operations. Equipment can be tested through weights and more. If a fall arrest system is in use, according to OSHA a weight of 300 pounds plus or minus five pounds should be used. No matter what kind of equipment you have in place, unless you test it regularly under the right circumstances, it could be completely useless for all you know.
Safety Gear: Your Options
To clarify, these are just a few of the options available to prevent falls. Safety nets are successful in preventing falls in areas with temporary floors in place, should scaffolds not be used and the fall distance be 25 feet or more. Slings are also quite successful in causing fall arrest — they come in several different types. These include endless, single, two, three, or four leg. These slings can come in the form of wire ropes, which are known for their durability. Whatever equipment gear you use, be sure to follow OSHA guidelines in determining its suitability.