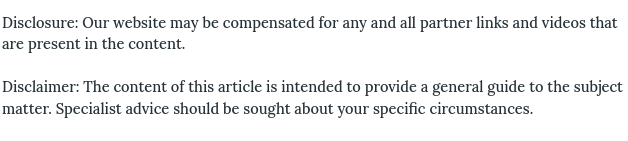
Induction heating has become one of the emerging processes that have improved the metal melting process making it quicker and more efficient. This is the reason why most mining companies are investing heavily in induction heating equipment. Metal melting has over the years been characterized by excessive heat loss. Considering that metals have different melting points, it has always been a challenge for some mining companies to ascertain the melting point of different metals. Compared to a conventional metal melting furnace, there are a lot of benefits of using the induction method as opposed to the traditional copper melting furnace. Many mining companies have abandoned the conventional copper melting furnace and the gold melting furnace and instead use induction heating equipment to melt the two metals. So why are mining companies abandoning the traditional melting furnace for the inductotherm melting furnace?
High Efficiency
The whole idea behind induction heating is to improve efficiency. Unlike traditional furnaces such as copper melting furnace where a lot of energy is loss during metal melting, induction heating takes place in a more controlled environment. After the melting procedure has been carried out in induction heating, an induction furnace can empty its contents completely. Since the temperatures in an induction furnace are extremely high, this ensures that there is separation of the metal in the induction furnace from any impurities. The possibility of all the contents of the final product being emptied means that it takes less time to prepare the induction furnace for another batch of metal to be smelted. This ultimately saves time and cost in the long term.
Smelting Process is Quicker
The traditional copper melting furnace was seen as working just fine until the introduction of an induction furnace. Currently, smelting metal takes less time and it is easy to know the exact temperature that a certain metal melts at keeping in mind that impurity also affect the melting point. Induction furnaces are relatively smaller compared to a traditional copper melting furnace. However, they are designed to be more effective in heating and the whole process takes place in an extremely controlled environment. The size should therefore not be used to presume that the amount of metal that can be melted in an induction furnace is relatively lower. It only takes a few hours to melt a certain metal compared to the period it would take to melt a similar metal in a conventional furnace. This means that you can melt metals in quick succession using an induction furnace.
Reduction of Waste
In induction heating, the process can be controlled at so many different levels. This provides for more accuracy in the process as well as minimizing wastage. One of the control procedures is the ability to control temperature. Depending on which metal you are melting, you can set the exact melting point of the metal. This means that since there is minimal or no heat loss, your metal will melt at that exact temperature. This strategy ensures that you do not heat your metal too much and end up wasting more energy on unnecessary heating. In addition to this, excessive heating of metal can lead to wastage which is why everything should be done in a more precise manner.