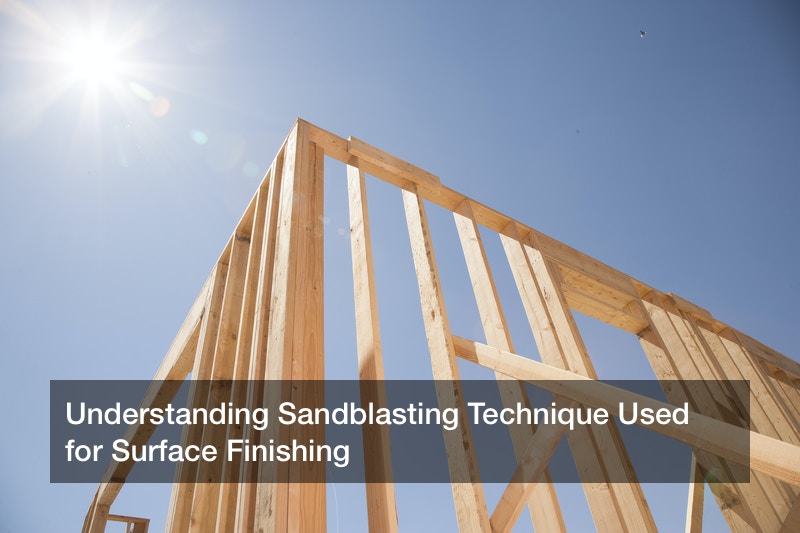
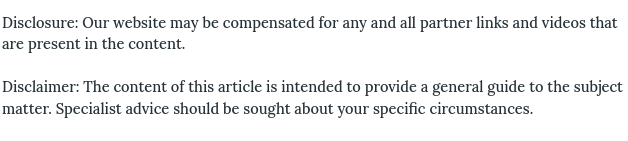
Sandblasting, also known as abrasive blasting or bead blasting is the process of using specialized machinery for burnishing, deburring, cleaning, or finishing surfaces. To get a better understanding of this technique, let’s look at a close example of sandpaper, which is commonly used to remove material from surfaces and make the surface smoother.
Although sandblasting uses a specialized tool, it’s the same theory as sandpaper. In blasting, a stream of air is forcibly propelled against a metal surface to thoroughly remove debris, dirt, paint and rust, resulting in smooth and engraved surfaces.
Primary Components of Sandblaster Machine
Sandblaster is the name given to the specialized machine used for blasting. The name is derived from the type of media used inside the abrasive blasting cabinet, which is sand. The four main components of blasting are:
- Abrasive Blasting Cabinet
- Blast system
- Air compressor
- Abrasive Media
Some blasting systems don’t use a cabinet, but to understand how this process works, we’ll look at blasting done inside a cabinet. Sandblasting cabinet is a container-like structure designed to contain key components — abrasive media(sand) and blasting system. Blast cabinets are available in different designs. You can get a plastic or steel one that has steel or plastic doors.
The cabinet design plays an integral role in determining the efficiency of the sandblaster. So choosing the best cabinet design is key to successfully sandblasting. First, consider the quality of the construction since it’s what will determine the weight of the parts you can put inside. More weight can make affect the stability of lesser built cabinets, especially if the fastening is bolts or pop rivets.
Another important thing to consider when selecting blasting cabinets designs are the side doors. As mentioned above, there are plastic and steel doors. A steel cabinet with steel doors is reliable, sturdy and durable in use as its fully sealed to ensure dust and debris remain inside the chamber. Any leaks can be messy and potentially dangerous. This is the same reason why plastic doors are discouraged because they ‘flex’ and leak over time.
What is sandblasting and how does it work?
Now that we have look at what is sandblasting and sandblaster are, we can move further ahead to how the process actually works. The two basic types of sandblasting are pressure, and suction or siphon or gravity fed.
- Siphon or Gravity fed sandblaster are perhaps the most basic blasting equipment available on the market today. This system works on the principle of gravity and atmospheric pressure which creates a suction effect that sucks abrasive media through a feed tube to the nozzle.
- Pressure fed sandblasters are designed for large production sandblasting and when compared to siphon fed machines, they are four times faster and effective. This has been made possible by the use of compressed air and a blasting process that also performs well at lower pressure. They use a pressure pot instead of suction to pressurize abrasive media before mixing with the compressed air inside the mixing chamber under high pressure. The airflow passes through the regulator first before entering the mixing chamber. This aims to lower the pressure at the nozzle.
When it comes to sandblasting service, there are several different types of abrasive media including shot blasting, beads glass, pumice, crush glass grit, aluminum oxide, garnet and plastic abrasives. Abrasive blasting can use either of the media to clean the surface for professional finishing provided there is enough air pressure. While the entire blasting process occurs in a special machine, it’s the media that does most of the job. Of course, there will be other factors such as the media, pressure and volume that will determine how effective and efficient the process will be.