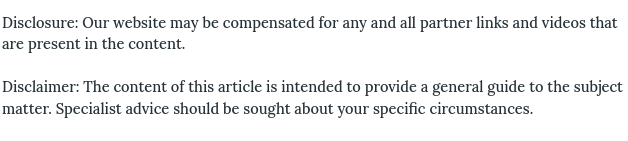
When traditional building methods are used for new commercial constructions, it takes more time than may be available. Then there’s the added financial costs associated with building materials such as cement, concrete, bricks, wood, and other necessary supplies. Given this, prefabricated and modular construction methods may be a welcome and cost-effective alternative for a variety of permanent or mobile structures.
Since modular units can be either permanent or mobile, they can provide an excellent options for warehouse offices and warehouse partitions to delineate work and storage areas. A mobile prefabricated office space can solve a variety of issues when companies need to move from one work site to another. There are other popular usages for prefabricated and modular constructions, according to a 2011 survey with industry professionals:
- Healthcare facilities: 49%
- Dormitories and other college buildings: 42%
- Manufacturing facilities: 42%
It’s interesting to note the results of FMI’s 2013 Prefabrication and Modularization in Construction Survey. According to the participating contractors, 40% stated that their ability to employ prefabricated and modular construction methods to their projects was an integral aspect of their company’s strategic initiative. This is a positive indicator of the future demand for these types of structures.
Some companies may use modular methods for their construction projects more often than others. The following percentage of industry professionals, however, indicated that they used them on some of their jobs:
- Engineers: 90%
- Contractors: 84%
- Architects: 76%
There are several reasons why prefabricated and modular construction methods may be the best or preferred option. A project can be completed in less time without sacrificing quality when these methods are used. This is due to the fact that 60% to 90% of prefabricated construction is handled in a controlled factory or warehouse environment. When projects are handled in this type of environment rather than on-site, workers, materials, and machinery don’t need to be transported to the same degree.
Less building materials are wasted during prefabricated and modular projects as well. The UK-based Waste and Resources Action Programme, for instance, indicated that it’s possible to experience a 90% reduction in waste. Given the level of waste that can occur with traditional building projects, this can make a significant impact on the overall cost of construction.
When companies opt for modular structures, a Building Industry Association of Philadelphia report found that this could potentially reduce construction costs by nine percent to 20%. This is also due to the reduced energy consumption that occurs during the actual building process, which is approximately 67%.
If your company or organization is interested in learning more about having a modular prefabricated office or other type of building constructed, a representative can provide you with more detailed information. In case you’re anticipating the need for a mobile prefabricated office space as opposed to a permanent one, this can also be discussed. When you need a larger office, work space, or housing, these units can be stacked on top of each other or attached side-by-side. Once you learn more about prefabricated modular units, you will realize that they are a versatile, time-saving, and cost-effective solution for a variety of purposes.