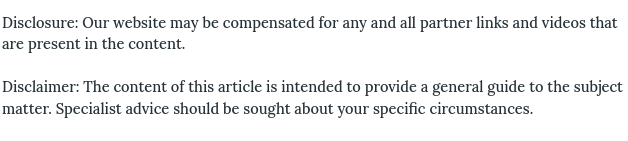

On a basic level, there are some things that an industrial engineer can’t go without. A polishing machine or lapping table machine is one of those things. Although they come in many different shapes and forms, polishing machines of quality can get the job done in a precise and quick manner. It’s not something that any company or individual should skimp on, either. Using an old and outdated polishing machine not only results in poor products, but potentially a good deal of damage to the individual operating the machine. Looking into the different kinds of polishing machines on the market, you can deduce what kind of machine is right for you and your purposes. There are many different options available, but by making an informed decision, you’ll ensure a safer and easier process for all.
What Is A Lapping Machine?
Lapping machines are machines that in short smooth out surfaces, depending on what level of smoothness the engineer needs. The process of lapping involves two surfaces being rubbed together, either by hand or by the machine itself. Lapping machines come in various different sizes, from table top units to 72″ plate configurations. Double Sided lapping machines can in fact process parts as thin as .002″ inches or with diameters of 20″. The kind of product that you need to create corresponds with one of the many different types of lapping machines on the market. But first, you need to know about what kind of end result you’re aiming for.
How Do You Measure Surface Roughness?
Surface roughness is defined by the different levels of height on a surface, usually on a minute level. Usually, roughness is expressed in “microinches”. If a surface exhibits an a Ra of 8, its peaks and valleys average at a maximum of 8 microinches over a given distance. Surface accuracy, on the other hand, is measured in Helium Light Bands, with one HLB measuring at .000011 inches. The typical accuracies are to one to three HLBs. Flatness is the usual goal in lapping, but at times people use the lapping process to achieve a concave surface, allowing for some variation in surface accuracy. So don’t bee surprised if the surface accuracy you achieve isn’t exactly perfect. It doesn’t have to be.
What Materials Are Using In Lapping Machines?
The kinds of materials used in lapping machines depend upon what kinds of results you want. For ceramic machine or finishing product, diamond is the best material. These products require edge-to-edge flatness, and the usual results include 11 millionths of an inch accuracy, with 1/20 wavelength being achievable. Diamond eliminates the hand-polishing step of lapping, and reduces the cycle by 30 minutes, saves $14.87 in costs, reduces waste, and reduces cleaning time. Clearly, diamond is the superior material to use if you need perfect precision.