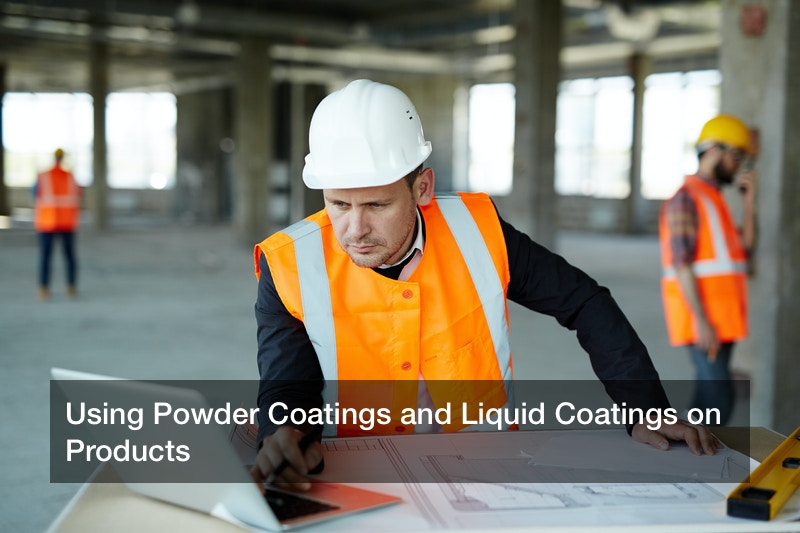
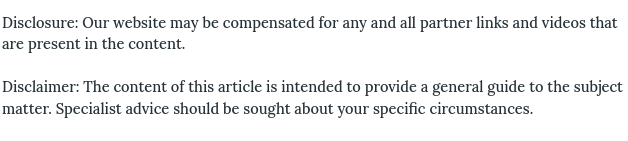
Many manufactured products for commercial use and industrial use need to have the proper finishing on their surfaces, often metal surfaces, and liquid coatings and powder coating are two major ways to apply paint and other aesthetic and protective coats onto metal products ranging from home appliances to bicycles. Appliances and other finished products, depending on their size, will be subject to either liquid coatings or powder coating for their professional finish. Why get a powder coating, or why should liquid coatings be used instead? Different products may call for different methods, and in some cases, liquid coatings are a must. In others, the best powder coating is the way to go.
On Powder Coating
The process of applying powder coatings instead of liquid coatings offers a number of distinctions and advantages over liquid coating, although powder coating methods are unlikely to entirely replace liquid coatings. Just what is powder coating? This is when a specialized spray gun uses a jet of pressurized air to put the finish on surfaces with powder, no liquids involved. Powder coating has emerged as a popular and effective coating method for many industries today, and being dry, it does not emit nearly as many volatile organic compounds (VOCs) that liquid coatings do. By now, powder coating has come to represent just over 15% of the entire finishing market, an impressive share. To get technical about it, powder coatings are categorized as 100% solids, but they do not actually require solvents in their formulation the way liquids coatings require solvents. Powder coating may find itself in a growing industry, meaning that this technology will spread even further; from 2016 to 2021, experts believe that demand for the coating industry will grow about 3% per year, on average, in the United States. Similarly, the worldwide powder coatings market value is set to reach a value of nearly $12.48 billion by the year 2020.
Powder coatings are appealing to those who work in the finishing market for a number of reasons, one of which is the relatively low pollution when compared to liquid coatings. Liquid paint and other finishers often give off a lot of VOCs, but it has been shown that powder finish does not release nearly as much, and this can cut down on labor costs since no pollution containment measures are necessary, and this also means that any company working with powder finishes will not have to be concerned about violating the EPA’s regulations about pollution of this nature. Overall, powder finishes can be considered environmentally friendly, since they do not actually use any solvents and give off very little VOC materials. Right now, it is the appliance industry that uses the most of the powder coating industry’s output, and one in three industrial parts are treated to powder coating. And right now, general industrial coating is the single biggest use of this technology, but in the near future, demand for powder coating for furniture is expected to grow 7.6% per year until the year 2020.
Liquid coatings are not totally obsolete, however. Some industrial and manufacturing services still work best with liquid coatings instead of the powder type, and for some items, the heat needed to fuse powder onto the surface is not practical. For many powder coat jobs, it is necessary to place the item inside an oven so that the powder can fuse onto the surface and form a skin, but some items are too large or too fragile or sensitive to heat for this, so liquid coatings are used on them instead, and this ensures that liquid coating industries will have a role to play in manufacturing in the coming years. A manufacturing company interested in working with a coating company can look for the right kind, and employees can search “powder coating Bay Area” for companies in the bay area of California, or “powder coating services Boston MA” to find something local.